Brayton Cycle – Turbine Engine
In 1872, an American engineer, George Bailey Brayton advanced the study of heat engines by patenting a constant pressure internal combustion engine, initially using vaporized gas but later using liquid fuels such as kerosene. This heat engine is known as “Brayton’s Ready Motor”. It means, the original Brayton engine used a piston compressor and piston expander instead of a gas turbine and gas compressor.
Today, modern gas turbine engines and airbreathing jet engines are also a constant-pressure heat engines, therefore we describe their thermodynamics by the Brayton cycle. In general, the Brayton cycle describes the workings of a constant-pressure heat engine.
It is the one of most common thermodynamic cycles that can be found in gas turbine power plants or in airplanes. In contrast to Carnot cycle, the Brayton cycle does not execute isothermal processes, because these must be performed very slowly. In an ideal Brayton cycle, the system executing the cycle undergoes a series of four processes: two isentropic (reversible adiabatic) processes alternated with two isobaric processes.
Since Carnot’s principle states that no engine can be more efficient than a reversible engine (a Carnot heat engine) operating between the same high temperature and low temperature reservoirs, a gas turbine based on the Brayton cycle must have lower efficiency than the Carnot efficiency.
A large single-cycle gas turbine typically produces for example 300 megawatts of electric power and has 35–40% thermal efficiency. Modern Combined Cycle Gas Turbine (CCGT) plants, in which the thermodynamic cycle of consists of two power plant cycles (e.g. the Brayton cycle and the Rankine cycle), can achieve a thermal efficiency of around 55%.
Types of Gas Turbines
In general, heat engines and also gas turbines are categorized according to a combustion location as:
- Turbines with internal combustion. Most gas turbines are internal combustion engines. In these turbines the high temperature is achieved by burning the fuel-air mixture in the combustion chamber.
- Turbines with external combustion. In these turbines, a heat exchanger is usually used and only clean medium with no combustion products travels through the power turbine. Since the turbine blades are not subjected to combustion products, much lower quality (and therefore cheaper) fuels are able to be used. These turbines have usually lower thermal efficiency than turbines with internal combustion.
Types of Brayton Cycle
Open Brayton Cycle (keywords)
Since most gas turbines are based on the Brayton cycle with internal combustion (e.g. jet engines), they are based on the open Brayton cycle. In this cycle, air from the ambient atmosphere is compressed to a higher pressure and temperature by the compressor. In the combustion chamber, air is heated further by burning the fuel-air mixture in the air flow. Combustion products and gases expand in the turbine either to near atmospheric pressure (engines producing mechanical energy or electrical energy) or to a pressure required by the jet engines. The open Brayton cycle means that the gases are discharged directly into the atmosphere.
Closed Brayton Cycle
In a closed Brayton cycle working medium (e.g. helium) recirculates in the loop and the gas expelled from the turbine is reintroduced into the compressor. In these turbines, a heat exchanger (external combustion) is usually used and only clean medium with no combustion products travels through the power turbine. The closed Brayton cycle is used, for example, in closed-cycle gas turbine and high-temperature gas cooled reactors.
Reverse Brayton Cycle – Brayton Refrigeration Cycle
A Brayton cycle that is driven in reverse direction is known as the reverse Brayton cycle. Its purpose is to move heat from colder to hotter body, rather than produce work. In compliance with the second law of thermodynamics, Heat cannot spontaneously flow from cold system to hot system without external work being performed on the system. Heat can flow from colder to hotter body, but only when forced by an external work. This is exactly what refrigerators and heat pumps accomplish. These are driven by electric motors requiring work from their surroundings to operate. One of possible cycles is a reverse Brayton cycle, which is similar to the ordinary Brayton cycle but it is driven in reverse, via net work input. This cycle is also known as the gas refrigeration cycle or Bell Coleman cycle. This type of cycle is widely used in jet aircrafts for air conditioning systems using air from the engine compressors. It is also widely used in the LNG industry where the largest reverse Brayton cycle is for subcooling LNG using 86 MW of power from a gas turbine-driven compressor and nitrogen refrigerant.
Brayton Cycle – Processes
In a closed ideal Brayton cycle, the system executing the cycle undergoes a series of four processes: two isentropic (reversible adiabatic) processes alternated with two isobaric processes:
closed Brayton cycle Isentropic compression (compression in a compressor) – The working gas (e.g. helium) is compressed adiabatically from state 1 to state 2 by the compressor (usually an axial-flow compressor). The surroundings do work on the gas, increasing its internal energy (temperature) and compressing it (increasing its pressure). On the other hand the entropy remains unchanged. The work required for the compressor is given by WC = H2 – H1.
- Isobaric heat addition (in a heat exchanger) – In this phase (between state 2 and state 3) there is a constant-pressure heat transfer to the gas from an external source, since the chamber is open to flow in and out. In an open ideal Brayton cycle, the compressed air then runs through a combustion chamber, where fuel is burned and air or another medium is heated (2 → 3). It is a constant-pressure process, since the chamber is open to flow in and out. The net heat added is given by Qadd = H3 – H2
- Isentropic expansion (expansion in a turbine) – The compressed and heated gas expands adiabatically from state 3 to state 4 in a turbine. The gas does work on the surroundings (blades of the turbine) and loses an amount of internal energy equal to the work that leaves the system. The work done by turbine is given by WT = H4 – H3. Again the entropy remains unchanged.
- Isobaric heat rejection (in a heat exchanger) – In this phase the cycle completes by a constant-pressure process in which heat is rejected from the gas. The working gas temperature drops from point 4 to point 1. The net heat rejected is given by Qre = H4 – H1
During a Brayton cycle, work is done on the gas by the compressor between states 1 and 2 (isentropic compression). Work is done by the gas in the turbine between stages 3 and 4 (isentropic expansion). The difference between the work done by the gas and the work done on the gas is the net work produced by the cycle and it corresponds to the area enclosed by the cycle curve (in pV diagram).
As can be seen, it is convenient to use enthalpy or specific enthalpy and to express the first law in terms of enthalpy in analysis of this thermodynamic cycle. This form of the law simplifies the description of energy transfer. At constant pressure, the enthalpy change equals the energy transferred from the environment through heating:
Isobaric process (Vdp = 0):
dH = dQ → Q = H2 – H1
At constant entropy, i.e. in isentropic process, the enthalpy change equals the flow process work done on or by the system:
Isentropic process (dQ = 0):
dH = Vdp → W = H2 – H1
See also: Why power engineers use enthalpy? Answer: dH = dQ + Vdp
Isentropic Process
An isentropic process is a thermodynamic process, in which the entropy of the fluid or gas remains constant. It means the isentropic process is a special case of an adiabatic process in which there is no transfer of heat or matter. It is a reversible adiabatic process. The assumption of no heat transfer is very important, since we can use the adiabatic approximation only in very rapid processes.
Isentropic Process and the First Law
For a closed system, we can write the first law of thermodynamics in terms of enthalpy:
dH = dQ + Vdp
or
dH = TdS + Vdp
Isentropic process (dQ = 0):
dH = Vdp → W = H2 – H1 → H2 – H1 = Cp (T2 – T1) (for ideal gas)
Isentropic Process of the Ideal Gas
The isentropic process (a special case of adiabatic process) can be expressed with the ideal gas law as:
pVκ = constant
or
p1V1κ = p2V2κ
in which κ = cp/cv is the ratio of the specific heats (or heat capacities) for the gas. One for constant pressure (cp) and one for constant volume (cv). Note that, this ratio κ = cp/cv is a factor in determining the speed of sound in a gas and other adiabatic processes.
Isobaric Process
An isobaric process is a thermodynamic process, in which the pressure of the system remains constant (p = const). The heat transfer into or out of the system does work, but also changes the internal energy of the system.
Since there are changes in internal energy (dU) and changes in system volume (∆V), engineers often use the enthalpy of the system, which is defined as:
H = U + pV
Isobaric Process and the First Law
The classical form of the first law of thermodynamics is the following equation:
dU = dQ – dW
In this equation dW is equal to dW = pdV and is known as the boundary work. In an isobaric process and the ideal gas, part of heat added to the system will be used to do work and part of heat added will increase the internal energy (increase the temperature). Therefore it is convenient to use the enthalpy instead of the internal energy.
Isobaric process (Vdp = 0):
dH = dQ → Q = H2– H1
At constant entropy, i.e. in isentropic process, the enthalpy change equals the flow process work done on or by the system.
Isobaric Process of the Ideal Gas
The isobaric process can be expressed with the ideal gas law as:
or
On a p-V diagram, the process occurs along a horizontal line (called an isobar) that has the equation p = constant.
See also: Charles’s Law
Brayton Cycle – pV, Ts diagram
The Brayton cycle is often plotted on a pressure volume diagram (pV diagram) and on a temperature-entropy diagram (Ts diagram).
When plotted on a pressure volume diagram, the isobaric processes follow the isobaric lines for the gas (the horizontal lines), adiabatic processes move between these horizontal lines and the area bounded by the complete cycle path represents the total work that can be done during one cycle.
The temperature-entropy diagram (Ts diagram) in which the thermodynamic state is specified by a point on a graph with specific entropy (s) as the horizontal axis and absolute temperature (T) as the vertical axis. Ts diagrams are a useful and common tool, particularly because it helps to visualize the heat transfer during a process. For reversible (ideal) processes, the area under the T-s curve of a process is the heat transferred to the system during that process.
Thermal Efficiency of Brayton Cycle
In general the thermal efficiency, ηth, of any heat engine is defined as the ratio of the work it does, W, to the heat input at the high temperature, QH.
The thermal efficiency, ηth, represents the fraction of heat, QH, that is converted to work. Since energy is conserved according to the first law of thermodynamics and energy cannot be be converted to work completely, the heat input, QH, must equal the work done, W, plus the heat that must be dissipated as waste heat QC into the environment. Therefore we can rewrite the formula for thermal efficiency as:
This is very useful formula, but here we express the thermal efficiency using the first law in terms of enthalpy.
To calculate the thermal efficiency of the Brayton cycle (single compressor and single turbine) engineers use the first law of thermodynamics in terms of enthalpy rather than in terms of internal energy.
The first law in terms of enthalpy is:
dH = dQ + Vdp
In this equation the term Vdp is a flow process work. This work, Vdp, is used for open flow systems like a turbine or a pump in which there is a “dp”, i.e. change in pressure. There are no changes in control volume. As can be seen, this form of the law simplifies the description of energy transfer.
There are expressions in terms of more familiar variables such as temperature and pressure:
dH = CpdT + V(1-αT)dp
Where Cp is the heat capacity at constant pressure and α is the coefficient of (cubic) thermal expansion. For ideal gas αT = 1 and therefore:
dH = CpdT
At constant pressure, the enthalpy change equals the energy transferred from the environment through heating:
Isobaric process (Vdp = 0):
dH = dQ → Q = H3 – H2 → H3 – H2 = Cp (T3 – T2)
At constant entropy, i.e. in isentropic process, the enthalpy change equals the flow process work done on or by the system:
Isentropic process (dQ = 0):
dH = Vdp → W = H4 – H3 → H4 – H3 = Cp (T4 – T3)
The enthalpy can be made into an intensive, or specific, variable by dividing by the mass. Engineers use the specific enthalpy in thermodynamic analysis more than the enthalpy itself.
Now, let assume the ideal Brayton cycle that describes the workings of a constant pressure heat engine. Modern gas turbine engines and airbreathing jet engines also follow the Brayton cycle. This cycle consist of four thermodynamic processes:
Brayton Cycle – Ts diagram isentropic compression – ambient air is drawn into the compressor, where it is pressurized (1 → 2). The work required for the compressor is given by WC = H2 – H1.
- isobaric heat addition – the compressed air then runs through a combustion chamber, where fuel is burned and air or another medium is heated (2 → 3). It is a constant-pressure process, since the chamber is open to flow in and out. The net heat added is given by Qadd = H3 – H2
- isentropic expansion – the heated, pressurized air then expands on turbine, gives up its energy. The work done by turbine is given by WT = H4 – H3
- isobaric heat rejection – the residual heat must be rejected in order to close the cycle. The net heat rejected is given by Qre = H4 – H1
As can be seen, we can fully describe and calculate such cycles (similarly for Rankine cycle) using enthalpies.
The thermal efficiency of such simple Brayton cycle, for ideal gas and in terms of specific enthalpies can now be expressed in terms of the temperatures:
where
- WT the work done by the gas in the turbine
- WC the work done on the gas in the compressor
- cp is the heat capacity ratio
Pressure Ratio – Brayton Cycle – Gas Turbine
The thermal efficiency in terms of the compressor pressure ratio (PR = p2/p1), which is the parameter commonly used:
In general, increasing the pressure ratio is the most direct way to increase the overall thermal efficiency of a Brayton cycle, because the cycle approaches the Carnot cycle.
According to Carnot’s principle higher efficiencies can be attained by increasing the temperature of the gas.
But there are also limits on the pressure ratios that can be used in the cycle. The highest temperature in the cycle occurs at the end of the combustion process, and it is limited by the maximum temperature that the turbine blades can withstand. As usual, metallurgical considerations (about 1700 K) place an upper limits on thermal efficiency.
Consider the effect of compressor pressure ratio on thermal efficiency when the turbine inlet temperature is restricted to the maximum allowable temperature. There are two Ts diagrams of Brayton cycles having the same turbine inlet temperature but different compressor pressure ratios on the picture. As can be seen for a fixed-turbine inlet temperature, the net work output per cycle (Wnet = WT – WC) decreases with the pressure ratio (Cycle A). But the Cycle A has the greater efficiency.
On the other hand, the Cycle B has a larger net work output per cycle (enclosed area in the diagram) and thus the greater net work developed per unit of mass flow. The work produced by the cycle times a mass flow rate through the cycle is equal to the power output produced by the gas turbine.
Therefore with less work output per cycle (Cycle A), a larger mass flow rate (thus a larger system) is needed to maintain the same power output, which may not be economical. This is the key consideration in design of gas turbine, since here engineers must balance the thermal efficiency and the compactness. In most common designs, the pressure ratio of a gas turbine ranges from about 11 to 16.
Thermal Efficiency Improvement – Brayton Cycle
There are several methods, how can be the thermal efficiency of the Brayton cycle improved. Assuming that the maximum temperature is limited by metallurgical consideration, these methods are:
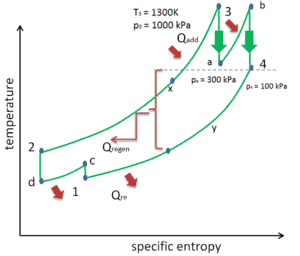
Reheat, Intercooling and Regeneration in Brayton Cycle
As was discussed reheat and intercooling are complementary with heat regeneration. By itself, they would not necessarily increase the thermal efficiency, however, when intercooling or reheat is used in conjunction with heat regeneration, a significant increase in thermal efficiency can be achieved and the net work output is also increased. This requires a gas turbine with two stages of compression and two turbine stages.
Isentropic Efficiency – Turbine, Compressor
Most steady-flow devices (turbines, compressors, nozzles) operate under adiabatic conditions, but they are not truly isentropic but are rather idealized as isentropic for calculation purposes. We define parameters ηT, ηC, ηN, as a ratio of real work done by device to work by device when operated under isentropic conditions (in case of turbine). This ratio is known as the Isentropic Turbine/Compressor/Nozzle Efficiency.
See also: Irreversibility of Natural Processes
These parameters describe how efficiently a turbine, compressor or nozzle approximates a corresponding isentropic device. This parameter reduces the overall efficiency and work output. For turbines, the value of ηT is typically 0.7 to 0.9 (70–90%).
Brayton Cycle – Problem with Solution
Let assume the closed Brayton cycle, which is the one of most common thermodynamic cycles that can be found in modern gas turbine engines. In this case assume a helium gas turbine with single compressor and single turbine arrangement. One of key parameters of such engines is the maximum turbine inlet temperature and the compressor pressure ratio (PR = p2/p1) which determines the thermal efficiency of such engine.
In this turbine the high-pressure stage receives gas (point 3 at the figure) from a heat exchanger:
- p3 = 6.7 MPa;
- T3 = 1190 K (917°C))
- the isentropic turbine efficiency is ηT = 0.91 (91%)
and exhaust it to another heat exchanger, where the outlet pressure is (point 4):
- p4 = 2.78 MPa
- T4,is = ?
Thus the compressor pressure ratio is equal to PR = 2.41. Moreover we know, that the compressor receives gas (point 1) at the figure:
- p1 = 2.78 MPa;
- T1 = 299 K (26°C)
- the isentropic compressor efficiency ηK = 0.87 (87%).
The heat capacity ratio, , for helium is equal to =cp/cv=1.66
- the heat added by the heat exchanger (between 2 → 3)
- the compressor outlet temperature of the gas (T2,is)
- the real work done on this compressor, when the isentropic compressor efficiency is ηK = 0.87 (87%)
- the turbine outlet temperature of the gas (T4,is)
- the real work done by this turbine, when the isentropic turbine efficiency is ηT = 0.91 (91%)
- the thermal efficiency of this cycle
Solution:
1) + 2)
From the first law of thermodynamics, the net heat added is given by Qadd,ex = H3 – H2 [kJ] or Qadd = Cp.(T3-T2s), but in this case we do not know the temperature (T2s) at the outlet of the compressor. We will solve this problem in intensive variables. We have to rewrite the previous equation (to include ηK) using the term (+h1 – h1) to:
Qadd = h3 – h2 = h3 – h1 – (h2s – h1)/ηK [kJ/kg]
Qadd = cp(T3-T1) – (cp(T2s-T1)/ηK)
Then we will calculate the temperature, T2s, using p, V, T Relation (from Ideal Gas Law) for adiabatic process between (1 → 2).
In this equation the factor for helium is equal to =cp/cv=1.66. From the previous equation follows that the compressor outlet temperature, T2s, is:
Qadd = cp(T3-T1) – (cp(T2s-T1)/ηK) = 5200.(1190 – 299) – 5200.(424-299)/0.87 = 4.633 MJ/kg – 0.747 MJ/kg = 3.886 MJ/kg
3)
The work done on the gas by the compressor in the isentropic compression process is:
WC,s = cp (T2s – T1) = 5200 x (424 – 299) = 0.650 MJ/kg
The real work done on the gas by the compressor in the adiabatic compression is then:
WC,real = cp (T2s – T1). ηC = 5200 x (424 – 299) / 0.87 = 0.747 MJ/kg
4)
The turbine outlet temperature of the gas, T4,is, can be calculated using the same p, V, T Relation as in 2) but between states 3 and 4:
From the previous equation follows that the outlet temperature of the gas, T4,is, is:
5)
The work done by gas turbine in the isentropic expansion is then:
WT,s = cp (T3 – T4s) = 5200 x (1190 – 839) = 1.825 MJ/kg
The real work done by gas turbine in the adiabatic expansion is then:
WT,real = cp (T3 – T4s) . ηT = 5200 x (1190 – 839) x 0.91 = 1.661 MJ/kg
6)
As was derived in the previous section, the thermal efficiency of an ideal Brayton cycle is a function of pressure ratio and κ:
therefore
ηth = 0.295 = 29.5%
The thermal efficiency can be also calculated using the work and the heat (without ηK):
ηth,s = (WT,s – WC,s) / Qadd,s = (1.825 – 0.650) / 3.983 = 0.295 = 29.5%
Finally, the thermal efficiency including isentropic turbine/compressor efficiency is:
ηth,real = (WT,real – WC,real) / Qadd = (1.661 – 0.747) / 3.886 = 0.235 = 23.5%
We hope, this article, Brayton Cycle – Gas Turbine Engine, helps you. If so, give us a like in the sidebar. Main purpose of this website is to help the public to learn some interesting and important information about thermal engineering.