Direct contact condensation
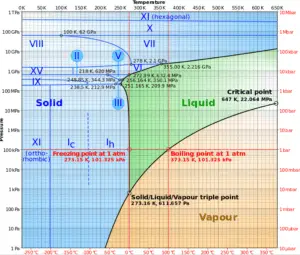
Source: wikipedia.org CC BY-SA
Similarly as in the previous chapter, in this chapter we will discuss heat transfer with phase change, but in this case we will discuss condensation of gas phase (vapor-to-liquid phase change).
In general, condensation is the change of the physical state of matter from gas phase into liquid phase, and is the reverse of vaporisation. Flow processes associated with condensation on a solid surface are almost a mirror image of those involved in boiling. Condensation occurs when the temperature of a vapor is reduced below its saturation temperature or when the pressure of a vapor is increased above its saturation parameters (see phase diagram of water).
Direct contact condensation, DCC, occurs when vapor is brought into contact with a cold liquid. As in jet condensers, the cooling water is sprayed on the exhaust steam and there is direct contact between the exhaust steam and cooling water. The process of condensation is very fast and efficient, but here cooling water and condensed steam are mixed up. The advantages of direct contact condensation over the conventional processes using metallic transfer surfaces are due to the relative simplicity of design, less corrosion and scaling problems, lower maintenance costs, higher specific transfer areas, and higher transfer rates. Despite these advantages jet condensers are not usual in thermal power plants especially due to the loss of condensate.
Condensation in Pressurizer
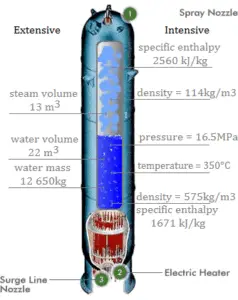
A pressurizer is a component of a pressurized water reactor. Pressure in the primary circuit of PWRs is maintained by a pressurizer, a separate vessel that is connected to the primary circuit (hot leg) and partially filled with water which is heated to the saturation temperature (boiling point) for the desired pressure by submerged electrical heaters. Temperature in the pressurizer can be maintained at 350 °C (662 °F), which gives a subcooling margin (the difference between the pressurizer temperature and the highest temperature in the reactor core) of 30 °C. Subcooling margin is very important safety parameter of PWRs, since the boiling in the reactor core must be excluded. The basic design of the pressurized water reactor includes such requirement that the coolant (water) in the reactor coolant system must not boil. To achieve this, the coolant in the reactor coolant system is maintained at a pressure sufficiently high that boiling does not occur at the coolant temperatures experienced while the plant is operating or in an analyzed transient.
Functions
Pressure in the pressurizer is controlled by varying the temperature of the coolant in the pressurizer. For these purposes two systems are installed. Water spray system and electrical heaters system. Volume of the pressurizer (tens of cubic meters) is filled with water on saturation parameters and steam. The water spray system (relatively cool water – from cold leg) can decrease the pressure in the vessel by condensing the steam on water droplets sprayed in the vessel. Since vapor is brought into contact with a cold liquid, in this case, we are talking about direct contact condensation. On the other hand the submerged electrical heaters are designed to increase the pressure by evaporation the water in the vessel. Water pressure in a closed system tracks water temperature directly; as the temperature goes up, pressure goes up.
We hope, this article, Direct contact condensation, helps you. If so, give us a like in the sidebar. Main purpose of this website is to help the public to learn some interesting and important information about thermal engineering.