Film Condensation
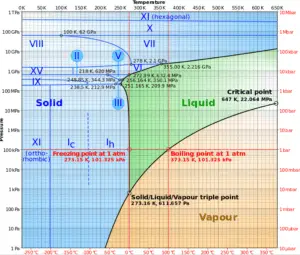
Source: wikipedia.org CC BY-SA
Similarly as in the previous chapter, in this chapter we will discuss heat transfer with phase change, but in this case we will discuss condensation of gas phase (vapor-to-liquid phase change).
In general, condensation is the change of the physical state of matter from gas phase into liquid phase, and is the reverse of vaporisation. Flow processes associated with condensation on a solid surface are almost a mirror image of those involved in boiling. Condensation occurs when the temperature of a vapor is reduced below its saturation temperature or when the pressure of a vapor is increased above its saturation parameters (see phase diagram of water).
In film condensation, the condensate wets the surface and forms a liquid film on the surface that slides down under the influence of gravity. Film condensation results in low heat transfer rates as the film of condensate impedes the heat transfer. The thickness of the film formed depends on many parameters including orientation of the surface, viscosity, rate of condensation etc. The film increases a thermal resistance to heat flow between the surface and the vapour. The rate of heat transfer is reduced because of this resistance.
Condensation in Power Plants – Main Condensator
The main steam condenser (MC) system is designed to condense and deaerate the exhaust steam from the main turbine and provide a heat sink for the turbine bypass system. The exhausted steam from the LP turbines is condensed by passing over tubes containing water from the cooling system. There is a main condenser unit under each LP turbine, usually below the turbine with its axis perpendicular to the turbine axis. Since nuclear power plants usually contain also an auxiliary condenser (e.g. to condense steam from steam driven feedwater pumps), engineers use the term “main condenser“.
See also: Main Condenser
The condenser must maintain a sufficient low vacuum in order to increase the power plant efficiency. The vacuum pumps maintain a sufficient vacuum in the condenser by extracting air and uncondensed gases. The lowest feasible condenser pressure is the saturation pressure corresponding to the ambient temperature (e.g. absolute pressure of 0.008 MPa, which corresponds to 41.5°C). Note that, there is always a temperature difference between (around ΔT = 14°C) the condenser temperature and the ambient temperature, which originates from finite size and efficiency of condensers. Since neither the condenser is 100% efficient heat exchanger, there is always a temperature difference between the saturation temperature (secondary side) and the temperature of the coolant in the cooling system. Moreover, there is a design inefficiciency, which decreases the overall efficiency of the turbine. Ideally the steam exhausted into the condenser would have no subcooling. But real condensers are designed to subcool the liquid by a few degrees of Celsius in order to avoid the suction cavitation in the condensate pumps.
The steam condensers are broadly classified into two types:
- Surface condensers (or non-mixing type condensers). In surface condensers, there is no direct contact between the exhaust steam and the cooling water.
- Jet condensers (or mixing type condensers). In jet condensers there is direct contact between the exhaust steam and cooling water.
We hope, this article, Film Condensation, helps you. If so, give us a like in the sidebar. Main purpose of this website is to help the public to learn some interesting and important information about thermal engineering.