Types of Heat Engines
In general, heat engines are categorized according to a combustion location as:
- External combustion engine. For example, steam engines are external combustion engines, where the working fluid is separate from the combustion products.
- Internal combustion engine. Typical example of internal combustion engine is an engine used in automobile, in which the high temperature is achieved by burning the gasoline-air mixture in the cylinder itself.
The detailed categorization is based on a working fluid used in thermodynamic cycle:
- Gas Cycles. In these cycles the working fluid is always a gas. The Otto cycle and the Diesel cycle (used is automobiles) are also typical examples of gas-only cycles. Modern gas turbine engines and airbreathing jet engines also based on the gas-only cycle, they follow the Brayton cycle.
- Liquid Cycles. Liquid-only cycles are rather exotic. In these cycles the working fluid is always a liquid. The Malone liquid engine is an example of liquid-only cycle. The Malone liquid engine was a modification of the Stirling cycle, using water as the working fluid instead of gas
- Cycles with Phase Changes. Steam engines are typical examples of external engines with phase change of working fluid.
Example of Heat Engine
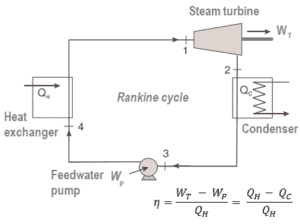
Steam engines and refrigerators are typical examples of external engines with phase change of working fluid. Typical thermodynamic cycle used to analyze this process is called the Rankine cycle, which usually uses water as the working fluid.
The Rankine cycle closely describes the processes in steam-operated heat engines commonly found in most of thermal power plants. The heat sources used in these power plants are usually the combustion of fossil fuels such as coal, natural gas, or also the nuclear fission.
A nuclear power plant (nuclear power station) looks like a standard thermal power station with one exception. The heat source in the nuclear power plant is a nuclear reactor. As is typical in all conventional thermal power stations the heat is used to generate steam which drives a steam turbine connected to a generator which produces electricity.
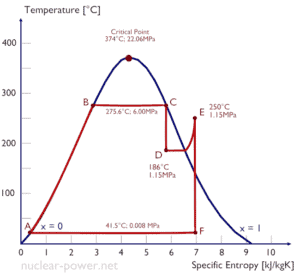
Typically most of nuclear power plants operates multi-stage condensing steam turbines. In these turbines the high-pressure stage receives steam (this steam is nearly saturated steam – x = 0.995 – point C at the figure; 6 MPa; 275.6°C) from a steam generator and exhaust it to moisture separator-reheater (point D). The steam must be reheated in order to avoid damages that could be caused to blades of steam turbine by low quality steam. The reheater heats the steam (point D) and then the steam is directed to the low-pressure stage of steam turbine, where expands (point E to F). The exhausted steam then condenses in the condenser and it is at a pressure well below atmospheric (absolute pressure of 0.008 MPa), and is in a partially condensed state (point F), typically of a quality near 90%.
In this case, steam generators, steam turbine, condensers and feedwater pumps constitute a heat engine, that is subject to the efficiency limitations imposed by the second law of thermodynamics. In ideal case (no friction, reversible processes, perfect design), this heat engine would have a Carnot efficiency of
= 1 – Tcold/Thot = 1 – 315/549 = 42.6%
where the temperature of the hot reservoir is 275.6°C (548.7K), the temperature of the cold reservoir is 41.5°C (314.7K). But the nuclear power plant is the real heat engine, in which thermodynamic processes are somehow irreversible. They are not done infinitely slowly. In real devices (such as turbines, pumps, and compressors) a mechanical friction and heat losses cause further efficiency losses.
Therefore nuclear power plants usually have efficiency about 33%. In modern nuclear power plants the overall thermodynamic efficiency is about one-third (33%), so 3000 MWth of thermal power from the fission reaction is needed to generate 1000 MWe of electrical power.
According to the Carnot’s principle higher efficiencies can be attained by increasing the temperature of the steam. But this requires an increase in pressures inside boilers or steam generators. However, metallurgical considerations place an upper limits on such pressures. From this point of view, supercritical water reactors are considered a promising advancement for nuclear power plants because of its high thermal efficiency (~45 % vs. ~33 % for current LWRs). SCWRs are operated at supercritical pressure (i.e. greater than 22.1 MPa).
We hope, this article, Type of Heat Engines – Example of Heat Engine, helps you. If so, give us a like in the sidebar. Main purpose of this website is to help the public to learn some interesting and important information about thermal engineering.