Thermal Efficiency of Brayton Cycle
In general the thermal efficiency, ηth, of any heat engine is defined as the ratio of the work it does, W, to the heat input at the high temperature, QH.
The thermal efficiency, ηth, represents the fraction of heat, QH, that is converted to work. Since energy is conserved according to the first law of thermodynamics and energy cannot be be converted to work completely, the heat input, QH, must equal the work done, W, plus the heat that must be dissipated as waste heat QC into the environment. Therefore we can rewrite the formula for thermal efficiency as:
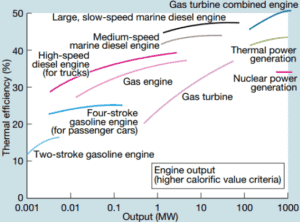
This is very useful formula, but here we express the thermal efficiency using the first law in terms of enthalpy.
To calculate the thermal efficiency of the Brayton cycle (single compressor and single turbine) engineers use the first law of thermodynamics in terms of enthalpy rather than in terms of internal energy.
The first law in terms of enthalpy is:
dH = dQ + Vdp
In this equation the term Vdp is a flow process work. This work, Vdp, is used for open flow systems like a turbine or a pump in which there is a “dp”, i.e. change in pressure. There are no changes in control volume. As can be seen, this form of the law simplifies the description of energy transfer.
There are expressions in terms of more familiar variables such as temperature and pressure:
dH = CpdT + V(1-αT)dp
Where Cp is the heat capacity at constant pressure and α is the coefficient of (cubic) thermal expansion. For ideal gas αT = 1 and therefore:
dH = CpdT
At constant pressure, the enthalpy change equals the energy transferred from the environment through heating:
Isobaric process (Vdp = 0):
dH = dQ → Q = H3 – H2 → H3 – H2 = Cp (T3 – T2)
At constant entropy, i.e. in isentropic process, the enthalpy change equals the flow process work done on or by the system:
Isentropic process (dQ = 0):
dH = Vdp → W = H4 – H3 → H4 – H3 = Cp (T4 – T3)
The enthalpy can be made into an intensive, or specific, variable by dividing by the mass. Engineers use the specific enthalpy in thermodynamic analysis more than the enthalpy itself.
Now, let assume the ideal Brayton cycle that describes the workings of a constant pressure heat engine. Modern gas turbine engines and airbreathing jet engines also follow the Brayton cycle. This cycle consist of four thermodynamic processes:
-
Brayton Cycle – Ts diagram isentropic compression – ambient air is drawn into the compressor, where it is pressurized (1 → 2). The work required for the compressor is given by WC = H2 – H1.
- isobaric heat addition – the compressed air then runs through a combustion chamber, where fuel is burned and air or another medium is heated (2 → 3). It is a constant-pressure process, since the chamber is open to flow in and out. The net heat added is given by Qadd = H3 – H2
- isentropic expansion – the heated, pressurized air then expands on turbine, gives up its energy. The work done by turbine is given by WT = H4 – H3
- isobaric heat rejection – the residual heat must be rejected in order to close the cycle. The net heat rejected is given by Qre = H4 – H1
As can be seen, we can fully describe and calculate such cycles (similarly for Rankine cycle) using enthalpies.
Thermal Efficiency – Brayton Cycle
The thermal efficiency of such simple Brayton cycle, for ideal gas can now be expressed in terms of the temperatures:
where
- WT the work done by the gas in the turbine
- WC the work done on the gas in the compressor
- cp is the heat capacity ratio
Pressure Ratio – Brayton Cycle – Gas Turbine
The thermal efficiency in terms of the compressor pressure ratio (PR = p2/p1), which is the parameter commonly used:
In general, increasing the pressure ratio is the most direct way to increase the overall thermal efficiency of a Brayton cycle, because the cycle approaches the Carnot cycle.
According to Carnot’s principle higher efficiencies can be attained by increasing the temperature of the gas.
But there are also limits on the pressure ratios that can be used in the cycle. The highest temperature in the cycle occurs at the end of the combustion process, and it is limited by the maximum temperature that the turbine blades can withstand. As usual, metallurgical considerations (about 1700 K) place an upper limits on thermal efficiency.

Consider the effect of compressor pressure ratio on thermal efficiency when the turbine inlet temperature is restricted to the maximum allowable temperature. There are two Ts diagrams of Brayton cycles having the same turbine inlet temperature but different compressor pressure ratios on the picture. As can be seen for a fixed-turbine inlet temperature, the net work output per cycle (Wnet = WT – WC) decreases with the pressure ratio (Cycle A). But the Cycle A has the greater efficiency.
On the other hand, the Cycle B has a larger net work output per cycle (enclosed area in the diagram) and thus the greater net work developed per unit of mass flow. The work produced by the cycle times a mass flow rate through the cycle is equal to the power output produced by the gas turbine.
Therefore with less work output per cycle (Cycle A), a larger mass flow rate (thus a larger system) is needed to maintain the same power output, which may not be economical. This is the key consideration in design of gas turbine, since here engineers must balance the thermal efficiency and the compactness. In most common designs, the pressure ratio of a gas turbine ranges from about 11 to 16.
Thermal Efficiency Improvement – Brayton Cycle
There are several methods, how can be the thermal efficiency of the Brayton cycle improved. Assuming that the maximum temperature is limited by metallurgical consideration, these methods are:
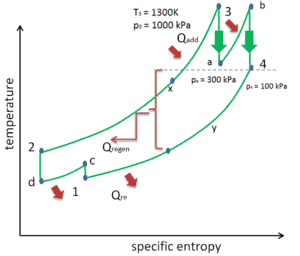
Reheat, Intercooling and Regeneration in Brayton Cycle
As was discussed reheat and intercooling are complementary with heat regeneration. By itself, they would not necessarily increase the thermal efficiency, however, when intercooling or reheat is used in conjunction with heat regeneration, a significant increase in thermal efficiency can be achieved and the net work output is also increased. This requires a gas turbine with two stages of compression and two turbine stages.
Isentropic Efficiency – Turbine, Compressor
Most steady-flow devices (turbines, compressors, nozzles) operate under adiabatic conditions, but they are not truly isentropic but are rather idealized as isentropic for calculation purposes. We define parameters ηT, ηC, ηN, as a ratio of real work done by device to work by device when operated under isentropic conditions (in case of turbine). This ratio is known as the Isentropic Turbine/Compressor/Nozzle Efficiency.
See also: Irreversibility of Natural Processes
These parameters describe how efficiently a turbine, compressor or nozzle approximates a corresponding isentropic device. This parameter reduces the overall efficiency and work output. For turbines, the value of ηT is typically 0.7 to 0.9 (70–90%).
We hope, this article, Thermal Efficiency – Brayton Cycle, helps you. If so, give us a like in the sidebar. Main purpose of this website is to help the public to learn some interesting and important information about thermal engineering.